Как эволюционировало трубное производство на Урале
Фото: пресс-служба ТМК В ближайшие годы трубную промышленность Свердловской области ждет переход на новый технологический уровень.
В ближайшие годы трубную промышленность Свердловской области ждет переход на новый технологический уровень. Дело в том, что Северский трубный завод (СТЗ) в Полевском планирует расширить применение на производстве «умных» технологий. Они позволят увеличить объемы выпуска продукции.
Процесс цифровизации на предприятии уже начался. Но внедряя передовые технологии, завод продолжает трепетно относиться к своему наследию. В год своего 285-летия предприятие решило показать, какой путь проделал Северский трубный завод за почти трехвековую историю. Взглянуть на это удалось корреспонденту URA.RU.
Историческое наследие
В середине XIX века сердцем завода была Северская домна. Это настоящий шедевр уральской промышленной архитектуры, в котором сегодня располагается уникальный в национальных масштабах музейный комплекс.
В первую очередь объект впечатляет своей необычной формой: восьмигранное здание с куполообразной крышей напоминает скорее храм, а не завод. Оно и неудивительно, ведь именно здесь больше века назад творилось таинство рождения чугуна.
Главная достопримечательность музея — 14,5-метровая доменная печь, построенная в 1860 году и подвергшаяся капитальному ремонту в 1898 году. Она ежедневно выпускала порядка 40 тонн чугуна.
«На самом верху печи размещается колошниковая площадка, с которой в печь загружали шихтовые материалы: железную руду, древесный уголь и известняк. Их поднимали на площадку гужевым транспортом по наклонным мостам и галереям», — рассказала экскурсовод музейного комплекса «Северская домна» Елена Липская.
Фото: пресс-служба ТМКЖидкий чугун выходил из доменной печи через отверстия — летки — в специальные желоба, проложенные по литейному двору. Там он накапливался в металлических изложницах и остывал.
Условия труда в те времена были тяжелыми. Пробивать отверстия для чугуна горновым приходилось вручную. Температура воздуха в этом месте превышала 1200 градусов, а все, что было на горновых — толстые варежки, валенки с деревянными колодками и кожаные фартуки. На колошниковой площадке ситуация была еще хуже: помимо невероятно высокой температуры рабочим приходилось терпеть ядовитые пары, которые выходили из доменной печи во время открытия створок засыпного аппарата.
Таким способом чугун на Северском заводе производили вплоть до 1934 года. Свою последнюю партию доменная печь выпустила в июне. Руководство предприятия приняло решение о закрытии домны в связи с развитием более прогрессивного мартеновского способа производства.
Завод 2.0
Производить трубы Северский завод начал в конце 1963 года, когда в эксплуатацию ввели трубоэлектросварочный цех. В 1976 году предприятие запустило мощный трубопрокатный цех с пилигримовыми станами, которые позволяли выпускать 320 тыс. тонн бесшовных труб в год. На этом оборудовании сотрудники СТЗ работали почти 40 лет.
«Предприятие развивается очень бурно. Особенно в последние 22 года, после того, как СТЗ стал частью Трубной Металлургической Компании. Тогда началась коренная реконструкция основного производства. У нас появились самые современные сталеплавильное производство и прокатный стан по выпуску бесшовных труб», — заявил управляющий директор СТЗ Дмитрий Марков.
Фото: пресс-служба ТМКСовременную линию по производству бесшовных труб с непрерывным станом установили в цехе в 2014 году. Она позволила подразделению нарастить объемы отгрузки выпускаемой продукции более чем на 60%.
Новые трубы выходят со стана каждые 55 секунд — это очень высокий темп. Но скорость не вредит качеству. На линии установлена совершенно новая система автоматики, которая позволяет детально настраивать стан и, соответственно, гарантировать высокое качество продукции.
Фото: пресс-служба ТМКСейчас в цехе работает почти 1400 человек, но сотрудников на производстве почти не видно. Создается впечатление, будто штанги-заготовки превращаются в трубы сами по себе. Дело в том, что выпуск труб действительно происходит в автоматическом режиме, однако за процессом тщательно следят специалисты завода. Параметры производства контролируются в реальном времени с помощью нескольких сотен специальных датчиков, установленных на протяжении всей производственной линии.
Первичная оценка происходит, когда трубы, раскаленные до 1100 градусов, попадают на стол охлаждения. После охлаждения их снова нагревают в печи и отправляют на калибровочный стан, чтобы придать трубам желаемый диаметр.
После проката трубы окончательно остывают на охладительном столе, проходят процесс правки на трубоправильной машине, разрезаются на заданные длины на пилах пакетной резки. На участках отделки трубы подвергаются необходимому контролю и проходят финишные операции, затем упаковку и отгрузку потребителю.
Фото: пресс-служба ТМКОсновные заказчики труб СТЗ — предприятия газовой и нефтяной промышленности. Обсадные трубы используются для добычи природных ресурсов, а нефтегазопроводные — для их транспортировки.
Планы на будущее
Сейчас перед заводом стоит цель увеличить объемы выпускаемой продукции. Достичь результата помогут проекты по цифровизации. На СТЗ, как и на других предприятиях ТМК, реализуется масштабная программа «Цифровое производство ТМК».
«Цифровая трансформация производства должна обеспечить существенное повышение эффективности и качества функционирования производственных систем на предприятиях ТМК. На горизонте до 2027 года компания завершит автоматизацию ключевых производственных систем и процесса накопления данных, что обеспечит в последующем технологический рывок от цифрового к „умному“ производству», — заявил технический директор ТМК Борис Пьянков.
В ближайшие годы трубную промышленность Свердловской области ждет переход на новый технологический уровень. Дело в том, что Северский трубный завод (СТЗ) в Полевском планирует расширить применение на производстве «умных» технологий. Они позволят увеличить объемы выпуска продукции. Процесс цифровизации на предприятии уже начался. Но внедряя передовые технологии, завод продолжает трепетно относиться к своему наследию. В год своего 285-летия предприятие решило показать, какой путь проделал Северский трубный завод за почти трехвековую историю. Взглянуть на это удалось корреспонденту URA.RU. Историческое наследие В середине XIX века сердцем завода была Северская домна. Это настоящий шедевр уральской промышленной архитектуры, в котором сегодня располагается уникальный в национальных масштабах музейный комплекс. В первую очередь объект впечатляет своей необычной формой: восьмигранное здание с куполообразной крышей напоминает скорее храм, а не завод. Оно и неудивительно, ведь именно здесь больше века назад творилось таинство рождения чугуна. Главная достопримечательность музея — 14,5-метровая доменная печь, построенная в 1860 году и подвергшаяся капитальному ремонту в 1898 году. Она ежедневно выпускала порядка 40 тонн чугуна. «На самом верху печи размещается колошниковая площадка, с которой в печь загружали шихтовые материалы: железную руду, древесный уголь и известняк. Их поднимали на площадку гужевым транспортом по наклонным мостам и галереям», — рассказала экскурсовод музейного комплекса «Северская домна» Елена Липская. Жидкий чугун выходил из доменной печи через отверстия — летки — в специальные желоба, проложенные по литейному двору. Там он накапливался в металлических изложницах и остывал. Условия труда в те времена были тяжелыми. Пробивать отверстия для чугуна горновым приходилось вручную. Температура воздуха в этом месте превышала 1200 градусов, а все, что было на горновых — толстые варежки, валенки с деревянными колодками и кожаные фартуки. На колошниковой площадке ситуация была еще хуже: помимо невероятно высокой температуры рабочим приходилось терпеть ядовитые пары, которые выходили из доменной печи во время открытия створок засыпного аппарата. Таким способом чугун на Северском заводе производили вплоть до 1934 года. Свою последнюю партию доменная печь выпустила в июне. Руководство предприятия приняло решение о закрытии домны в связи с развитием более прогрессивного мартеновского способа производства. Завод 2.0 Производить трубы Северский завод начал в конце 1963 года, когда в эксплуатацию ввели трубоэлектросварочный цех. В 1976 году предприятие запустило мощный трубопрокатный цех с пилигримовыми станами, которые позволяли выпускать 320 тыс. тонн бесшовных труб в год. На этом оборудовании сотрудники СТЗ работали почти 40 лет. «Предприятие развивается очень бурно. Особенно в последние 22 года, после того, как СТЗ стал частью Трубной Металлургической Компании. Тогда началась коренная реконструкция основного производства. У нас появились самые современные сталеплавильное производство и прокатный стан по выпуску бесшовных труб», — заявил управляющий директор СТЗ Дмитрий Марков. Современную линию по производству бесшовных труб с непрерывным станом установили в цехе в 2014 году. Она позволила подразделению нарастить объемы отгрузки выпускаемой продукции более чем на 60%. Новые трубы выходят со стана каждые 55 секунд — это очень высокий темп. Но скорость не вредит качеству. На линии установлена совершенно новая система автоматики, которая позволяет детально настраивать стан и, соответственно, гарантировать высокое качество продукции. Сейчас в цехе работает почти 1400 человек, но сотрудников на производстве почти не видно. Создается впечатление, будто штанги-заготовки превращаются в трубы сами по себе. Дело в том, что выпуск труб действительно происходит в автоматическом режиме, однако за процессом тщательно следят специалисты завода. Параметры производства контролируются в реальном времени с помощью нескольких сотен специальных датчиков, установленных на протяжении всей производственной линии. Первичная оценка происходит, когда трубы, раскаленные до 1100 градусов, попадают на стол охлаждения. После охлаждения их снова нагревают в печи и отправляют на калибровочный стан, чтобы придать трубам желаемый диаметр. После проката трубы окончательно остывают на охладительном столе, проходят процесс правки на трубоправильной машине, разрезаются на заданные длины на пилах пакетной резки. На участках отделки трубы подвергаются необходимому контролю и проходят финишные операции, затем упаковку и отгрузку потребителю. Основные заказчики труб СТЗ — предприятия газовой и нефтяной промышленности. Обсадные трубы используются для добычи природных ресурсов, а нефтегазопроводные — для их транспортировки. Планы на будущее Сейчас перед заводом стоит цель увеличить объемы выпускаемой продукции. Достичь результата помогут проекты по цифровизации. На СТЗ, как и на других предприятиях ТМК, реализуется масштабная программа «Цифровое производство ТМК». «Цифровая трансформация производства должна обеспечить существенное повышение эффективности и качества функционирования производственных систем на предприятиях ТМК. На горизонте до 2027 года компания завершит автоматизацию ключевых производственных систем и процесса накопления данных, что обеспечит в последующем технологический рывок от цифрового к „умному“ производству», — заявил технический директор ТМК Борис Пьянков. Юрий Петухов © Служба новостей «URA.RU»Последние новости
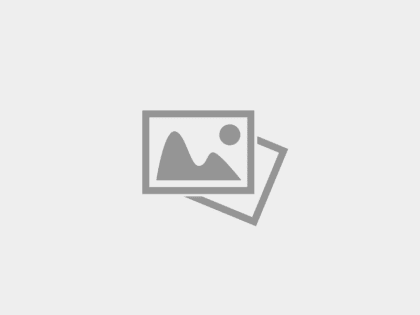
В Серове на основании заключения прокурора главный редактор газеты одного из предприятий города восстановлена на работе
Сотрудник Серовской городской прокуратуры в порядке ч. 3 ст. 45 ГПК РФ принял участие в рассмотрении судом гражданского дела по иску жительницы города о восстановлении на работе и взыскании вынужденного прогула.
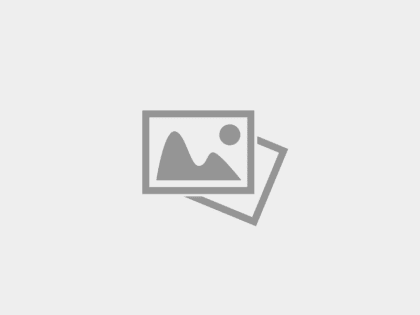
Врио губернатора Денис Паслер поздравил геологов и ветеранов отрасли с профессиональным праздником
Как отмечено в обращении, труд геологов ответственен и почётен, поскольку служит росту экономики,
Новый городской портал «Афиша Лесной»
На сайте можно узнать обо всех запланированных городских мероприятиях. А в ближайшее время на сайте появится информация не только о культурных, но и о спортивных событиях.
Куда пойти с детьми в Уфе: 10 весёлых мест на выходные
Идеи для семейного отдыха в столице Башкортостана — от активных игр до познавательных музеев